Here is a simple ANTI-THEFT ALARM AND HORN. It generates a loud alarm when there is an attempt of theft. When the intruder opens the door, the circuit senses the attempt of theft and after 2 minutes, the alarm will be activated. The time delay is provided to help the user to leave after arming with the device.
Voltage On Bargraph Display
Posted by Okla
Posted on 16:32
The LM3914 is a truly versatile component. Besides LEDs, only a few other components are needed to make the ‘bidirectional’ bargraph voltmeter shown here. The circuit is similar to a conventional bar display, but it offers a possibility to change the direction in which the LEDs are switched on. This may be useful, for example, when positive and negative voltages are measured. For a positive input voltage, the LEDs are switched on in the usual manner, that is, from D3 to D12, while for negative voltages, the LEDs are switched on in the opposite direction, from D12 to D3. Obviously, the negative voltage must be ‘rectified’, i.e. inverted, before the measurement.
A suitable circuit for this purpose is presented in the article ‘Absolute-value meter with polarity detector’ elsewhere in this website. A set of transistor switches (MOSFETs) controls the direction in which the LEDs light. When the control voltage is high (+6V, according to the schematics, but any voltage that is at least 3V higher than reference voltage will do), T1 and T4 are switched on, while the other two MOSFETs are off. In this way, the LM3194 is configured in the usual manner with the top end of the resistor network connected to the internal voltage reference and the low end connected to ground.
A suitable circuit for this purpose is presented in the article ‘Absolute-value meter with polarity detector’ elsewhere in this website. A set of transistor switches (MOSFETs) controls the direction in which the LEDs light. When the control voltage is high (+6V, according to the schematics, but any voltage that is at least 3V higher than reference voltage will do), T1 and T4 are switched on, while the other two MOSFETs are off. In this way, the LM3194 is configured in the usual manner with the top end of the resistor network connected to the internal voltage reference and the low end connected to ground.

As the input voltage rises, the comparators inside the LM3914 will cause the indicator LEDs to be switched on one by one, starting with D3. When the control voltage is lower than about –3V, T2 and T3 are switched on while T1 and T4 are off. Consequently, the ends of the resistor network are connected the other way around: the top end goes to ground and the low end, to the reference voltage. The first LED to be switched on will then be D12; i.e., the LEDs that forms the bargraph display light in the opposite direction. Although not documented by the manufacturer of the LM3914, this option works well, but only in bar mode (in dot mode, internal logic disables any lower-numbered LEDs when a higher-numbered LED s on, which obviously conflicts with our purposes).
To achieve good symmetry, an adjustable resistor is added to the voltage divider in the LM3914. Using a DVM, adjust the preset until the voltage across P1+R4 equals 1/11th part of Urefout. Sensitivity is determined with the ratio of resistors R5 and P2. If, for example, the reference voltage is set to 2.2 V by means of P2, there will be a voltage drop of 200 mV per resistor in the ladder network (including R4-P1). So, the first LED will switch on when the input voltage exceeds 200 mV, the second, at 400 mV, and so on, and the whole display will be on at 2 V. The circuit draws about 100 mA when all LEDs are switched on.
To achieve good symmetry, an adjustable resistor is added to the voltage divider in the LM3914. Using a DVM, adjust the preset until the voltage across P1+R4 equals 1/11th part of Urefout. Sensitivity is determined with the ratio of resistors R5 and P2. If, for example, the reference voltage is set to 2.2 V by means of P2, there will be a voltage drop of 200 mV per resistor in the ladder network (including R4-P1). So, the first LED will switch on when the input voltage exceeds 200 mV, the second, at 400 mV, and so on, and the whole display will be on at 2 V. The circuit draws about 100 mA when all LEDs are switched on.
Infra red Remote Control Tester
Posted by Okla
Posted on 16:29
As I was developing my IR Extender Circuit, I needed to find a way of measuring the relative intensities of different Infra red light sources. This circuit is the result of my research. I have used a photodiode, SFH2030 as an infra red sensor. A MOSFET opamp, CA3140 is used in the differential mode to amplify the pulses of current from the photodiode. LED1 is an ordinary coloured led which will light when IR radiation is being received.
The output of the opamp, pin 6 may be connected to a multimeter set to read DC volts. Infra red remote control strengths can be compared by the meter reading, the higher the reading, the stronger the infra red light. I aimed different remote control at the sensor from about 1 meter away when comparing results. For every microamp of current through the photodiode, about 1 volt is produced at the output. A 741 or LF351 will not work in this circuit. Although I have used a 12 volt power supply, a 9 volt battery will also work here.
Circuit diagram:
Circuit diagram:

Hydrophone Booster Amplifier HA2
Posted by Okla
Posted on 20:02

The HP series Hydrophone Booster Amplifier (HA2) amplifies low-level hydrophone signals over a wide range of frequencies. It has a minimum gain of 25dB and an input and output impedance of 50Ω. The HA2 is designed for use with either Precision Acoustics membrane hydrophone or Precision Acoustics HP Series Hydrophone Measurement System, which is shown in Fig 1.

Alternatively, the HA2 may be used when the acoustic signal is provided by a high output impedance hydrophone, such as a GEC-Marconi membrane device, or a conventional hydrophone. In this instance a BNC/MCX adaptor is used which connects directly to the HP Series Submersible Preamplifier, using it as a buffer amplifier, (i.e. the standard Precision Acoustic HP Series configuration shown in Fig 1 is used, but without the interchangeable probe).
The HA2 amplifier is straightforward to use but the following points should be noted:
- The output of the amplifier should be correctly terminated in 50Ω before operation.
Before Connecting the unit please read WARNING
To Connect | To Disconnect |
1 | Connect Output Load | 1 | Remove RF Input |
2 | Apply DC Voltage | 2 | Remove DC Volts |
3 | Apply RF Input | 3 | Remove Load |
Specification (HA2 Amplifier Only)
Voltage Gain = 25dB minimum
Bandwidth = 50kHz to 125MHz ±1.0dB
Maximum Output Level = 29dBm for 1dB compression (18.1V pk – pk into 50Ω load)
Input Impedance = Nominal 50Ω
Output Impedance Nominal 50Ω (VSWR 2:1)
Output Noise Level = Typically 70μV pk – pk (bandwidth 125MHz)
Noise Figure = Typically 10dB
Phase = Non-inverting
Terminations:
Front panel = Input BNC socket BNC Output socket
Rear panel Power Requirements = 28v dc output to supply DC Coupler 100/120/220/240V ac, 50 to 60Hz,
7.5W
Operating Temperature = 0 to 50°C
Size = (90mm × 205mm ×194mm)
Weight = 2.6kg
Bandwidth = 50kHz to 125MHz ±1.0dB
Maximum Output Level = 29dBm for 1dB compression (18.1V pk – pk into 50Ω load)
Input Impedance = Nominal 50Ω
Output Impedance Nominal 50Ω (VSWR 2:1)
Output Noise Level = Typically 70μV pk – pk (bandwidth 125MHz)
Noise Figure = Typically 10dB
Phase = Non-inverting
Terminations:
Front panel = Input BNC socket BNC Output socket
Rear panel Power Requirements = 28v dc output to supply DC Coupler 100/120/220/240V ac, 50 to 60Hz,
7.5W
Operating Temperature = 0 to 50°C
Size = (90mm × 205mm ×194mm)
Weight = 2.6kg
Copyright : Precision Acoustics March 2004
Railway Points Sequencer
Posted by Okla
Posted on 20:02
Dedicated variation rail fanatics using sophisticated train and points controllers regularly have the drawback that as their formats get greater and more advanced, the transformer offering power to the points does not have sufficient present to change a couple of points at the comparable time. The actuators within the points are designed for ac operation so it doesn’t assist via rectifying the provision and including reservoir capacitors, the coils can overheat and burn out if they get jammed throughout their shuttle (ac operation if actuality be told assists to beat friction in the mechanism). The circuit shown right here clear ups this drawback by means of using a sequencer to ensure than only one points actuator can be energetic at any time limit. During operation the controller will switch all the factors on one line concurrently normal, but the different connection to each and every coil is connected to the sequencer unit. This circuit will simplest enable present to flow through one coil at a time.
Circuit diagram :

The sequencer circuit consists of a 555 timer configured as an astable multivibrator clocking a 4017 Johnson counter the place the ten outputs are used to modify ten triacs in sequence, enough for ten units of factors. P1 alters the oscillator frequency of the 555 timer and can be adjusted in order that every time interval of the sequencer is lengthy enough to permit the points to modify.
The switching time varies depending on the type of factors however is usually between 1 s and 1.5 s. Any points that jam during swaping give out a characteristic humming noise in time to the swaping frequency so it makes them more straightforward to find. The eleventh output of the 4017 can be linked to an LED (together with a sequence resistor). This will flash to present a visual indication of the sequencers operation. Power for the circuit is provided through 15 V ac from the points transformer. The B80C1500 bridge rectifier (80 Vpiv, 1.5 A) and regulator IC1 produce a stabilised 12 V for the circuit. Current consumption is only a few milliamps.
http://www.ecircuitslab.com/2011/07/railway-points-sequencer.html
Baud Rate Generator
Posted by Okla
Posted on 20:01
In this text, an RC oscillator is used as a baud fee generator. If that you can be able to calibrate the frequency of such a circuit adequately competently (within a few percent) utilizing a frequency meter, it goes to work very neatly. However, it should smartly drift slightly after some time, and then…. Consequently, right here we current a small crystal-controlled oscillator. If you begin with a crystal frequency of two.45765 MHz and divide it by means of more than ones of 2, you may very effectively obtain the smartly-known baud charges of 9600, 4800, 2400, 600, 300, a hundred and fifty and seventy five. If you seem to be intently at this series, you are going to see that 1200 baud is lacking, because divider within the 4060 has no Q10 output!

If you don't want 1200 baud, this is not an issue. However, seeing that 1200 baud is utilized in observe more continuously than 600 baud, we've put a divide-by-two stage within the circuit after the 4060, within the type of a 74HC74 flip-flop. This yields a similar series of baud rates, through which 600 baud is missing. The trimmer is for the calibration purists; a 33 pF capacitor will frequently provide enough accuracy. The current consumption of this circuit may be very low (around 1mA), because of the usage of CMOS elements.
www.ecircuitslab.com
4 Bit Analogue to Digital Converter
Posted by Okla
Posted on 20:01
The operation of the converter is based on the weighted adding and transferring of the analogue input levels and the digital output levels. It consists of comparators and resistors. In theory, the number of bits is unlimited, but each bit needs a comparator and several coupling resistors. The diagram shows a 4-bit version. The value of the resistors must meet the following criteria:
- R1:R2 = 1:2;
- R3:R4:R5 = 1:2:4;
- R6:R7:R8:R9 = 1:2:4:8.
The linearity of the converter depends on the degree of precision of the value of the resistors with respect to the resolution of the converter, and on the accuracy of the threshold voltage of the comparators. This threshold level must be equal, or nearly so, to half the supply voltage. Moreover, the comparators must have as low an output resistance as possible and as high an input resistance with respect to the load resistors as feasible. Any deviation from these requirements affects the linearity of the converter adversely.
Circuit diagram:
4-Bit Analogue to Digital Converter Circuit Diagram
If the value of the resistors is not too low, the use of inverters with an FET (field-effect transistor) input leads to a near-ideal situation. In the present converter, complementary metal-oxide semiconductor (CMOS) inverters are used, which, in spite of their low gain, give a reasonably good performance. If standard comparators are used, take into account the output voltage range and make sure that the potential at their non-inverting inputs is set to half the supply voltage. If high accuracy is a must, comparators Type TLC3074 or similar should be used. This type has a totem-pole output. The non-inverting inputs should be interlinked and connected to the tap of a a divider consisting of two 10 kΩ resistors across the supply lines. It is essential that the converter is driven by a low-resistance source. If necessary, this can be arranged via a suitable op amp input buffer. The converter draws a current not exceeding 5 mA.
Source :www.ecircuitslab.com
Battery Juicer
Posted by Okla
Posted on 11:00
More and extra digital devices are portable and run off batteries. It is no surprise, then, that so many flat batteries find their way into the bin and frequently a lengthy way too early. When a collection of batteries can no longer run some tool as an example, a flashgun the cells will no lengthyer be necessarily completely discharged. If you put an it sounds as if unserviceable AA-size cell right into a radio-controlled clock with an LCD display it'll run for months if no longer yrs.
Of path now not every partially discharged cell can be put in a clock. The circuit offered here means that you simply can squeeze the closing Watt-second out of your batteries, offering a bright ‘night light’ - for free! The circuit features a TBA820M, an inexpensive audio power amplifier able to operating from an extraordinarily low supply voltage. Here it is hooked up as an astable multivibrator running at a frequency of round thirteen kHz. Together with the 2 diodes and electrolytic capacitor this forms a DC-DC converter which will nearly double the voltage from between 4 and eight series-connected AA-, C- or D-size cells, or from a PP3-style battery.
Circuit diagram:
Battery Juicer Circuit Diagram
The DC-DC converter is adopted by using a continuing present supply which forces the LED. This give protection tos the dear white LED: the voltages obtained from outdated batteries can vary significantly. With using the DC-DC converter and 20 mA steady present source a much greater range of usable enter voltages is performed, particularly useful on the decrease finish of the range when outdated batteries are used. With the steady present source by itself the white LED would no longer be thoroughly vibrant when run from low voltages.
An extra feature is the ‘automatic eye’. The LDR realizes when the traditional room lights is switched on or when the room is lit by way of sunlight: its resistance lowers. This reduces the UBE of the transistor below zero.7 V, the BC337 flips off and deactivates the LED. This extends further the lifetime of the outdated batteries. A further LDR across capacitor C cut backs the quiescent present of the circuit to simply 4mA (at 4V). Light from the white LED should in fact now not fall on the LDR, or the present saving perform won't work.
Author : W. Zeiller
IC 555 Design Note
Posted by Okla
Posted on 08:00
The popular Timer IC 555 is extensively used in short duration timing applications. IC 555 is a highly stable integrated circuit functioning as an accurate time delay generator and free running multivibrator. But one of the serious problem in 555 timer design is the false triggering of the circuit at power on or when voltage changes. The article describes how IC555 is designed perfectly to avoid false triggering.
555 IC pin functions
Pin1 Ground
Pin2 Trigger
Pin3 Output
Pin 4 Reset
Pin 5 Control voltage
Pin 6 Threshold
Pin 7 Discharge
Pin 8 Vcc
Functional aspects of pins
Trigger Pin 2
Usually pin2 of the IC is held high by a pull up resistor connected to Vcc. When a negative going pulse is applied to pin 2, the potential at pin 2 falls below 1/3 Vcc and the flip-flop switches on. This starts the timing cycle using the resistor and capacitor connected to pins 6 and 7.
Reset pin 4
Reset pin 4 can be controlled to reset the timing cycle. If pin 4 is grounded, IC will not be triggered. When pin4 becomes positive, IC becomes ready to start the timing cycle. Reset voltage is typically 0.7 volts and reset current 0.1 mA. In timer applications, reset pin should be connected to Vcc to get more than 0.7 volts.
Control Voltage pin 5
Pin5 can be used to control the working of IC by providing a DC voltage at pin5. This permits the control of the timing cycle manually or electronically. In monostable operation, the control pin5 is connected to ground through a 0.01 uF capacitor. This prevents the timing interval from being affected by AC or RF interference. In the Astable mode, by applying a variable DC voltage at pin 5 can change the output pulses to FM or PWM.
Threshold pin 6 and Discharge pin 7
These two inputs are used to connect the timing components- Resistor and Capacitor. The threshold comparator inside the IC is referenced at 2/3 Vcc and the trigger comparator is referenced at 1/3 Vcc. These two comparators control the internal Flip-Flop of the circuit to give High or Low output at pin 3.When a negative going pulse is applied to pin 2, the potential at pin2 drops below 1/3 Vcc and the trigger comparator switches on the Flip-Flop. This turns the output high. The timing comparator then charges through the timing resistor and the voltage in the timing capacitor increases to 2/3 Vcc.( The time delay depends on the value of the resistor and capacitor.
That is, higher values, higher time).When the voltage level in the capacitor increases above 2/3 Vcc, the threshold comparator resets the Flip-Flop and the output turns low. Capacitor then discharges through pin 7.Once triggered, the IC will not responds to further triggering until the timing cycle is completed. The time delay period is calculated using the formula T= 1.1 Ct Rt. Where Ct is the value of Capacitor in PF and Rt is the value of Resistor in Ohms. Time is in Seconds.
How to eliminate false triggering?
The circuit diagram shown below is the simple monostable using IC 555. To eliminate the false triggering resistor R1 and Capacitor C1 are connected to the reset pin 4 of the IC. So the reset pin is always high even if the supply voltage changes. Moreover capacitor C3 connected close to the Vcc pin 8 acts as a buffer to maintain stable supply voltage to pin 8. Using this design, it is easy to avoid false triggering to a certain extent.
555 IC pin functions
Pin1 Ground
Pin2 Trigger
Pin3 Output
Pin 4 Reset
Pin 5 Control voltage
Pin 6 Threshold
Pin 7 Discharge
Pin 8 Vcc
Functional aspects of pins
Trigger Pin 2
Usually pin2 of the IC is held high by a pull up resistor connected to Vcc. When a negative going pulse is applied to pin 2, the potential at pin 2 falls below 1/3 Vcc and the flip-flop switches on. This starts the timing cycle using the resistor and capacitor connected to pins 6 and 7.
Reset pin 4
Reset pin 4 can be controlled to reset the timing cycle. If pin 4 is grounded, IC will not be triggered. When pin4 becomes positive, IC becomes ready to start the timing cycle. Reset voltage is typically 0.7 volts and reset current 0.1 mA. In timer applications, reset pin should be connected to Vcc to get more than 0.7 volts.
Control Voltage pin 5
Pin5 can be used to control the working of IC by providing a DC voltage at pin5. This permits the control of the timing cycle manually or electronically. In monostable operation, the control pin5 is connected to ground through a 0.01 uF capacitor. This prevents the timing interval from being affected by AC or RF interference. In the Astable mode, by applying a variable DC voltage at pin 5 can change the output pulses to FM or PWM.
Threshold pin 6 and Discharge pin 7
These two inputs are used to connect the timing components- Resistor and Capacitor. The threshold comparator inside the IC is referenced at 2/3 Vcc and the trigger comparator is referenced at 1/3 Vcc. These two comparators control the internal Flip-Flop of the circuit to give High or Low output at pin 3.When a negative going pulse is applied to pin 2, the potential at pin2 drops below 1/3 Vcc and the trigger comparator switches on the Flip-Flop. This turns the output high. The timing comparator then charges through the timing resistor and the voltage in the timing capacitor increases to 2/3 Vcc.( The time delay depends on the value of the resistor and capacitor.
That is, higher values, higher time).When the voltage level in the capacitor increases above 2/3 Vcc, the threshold comparator resets the Flip-Flop and the output turns low. Capacitor then discharges through pin 7.Once triggered, the IC will not responds to further triggering until the timing cycle is completed. The time delay period is calculated using the formula T= 1.1 Ct Rt. Where Ct is the value of Capacitor in PF and Rt is the value of Resistor in Ohms. Time is in Seconds.
How to eliminate false triggering?
The circuit diagram shown below is the simple monostable using IC 555. To eliminate the false triggering resistor R1 and Capacitor C1 are connected to the reset pin 4 of the IC. So the reset pin is always high even if the supply voltage changes. Moreover capacitor C3 connected close to the Vcc pin 8 acts as a buffer to maintain stable supply voltage to pin 8. Using this design, it is easy to avoid false triggering to a certain extent.
555 Monostable circuit

A ready recknor to select timing resistor and capacitor

Theoretically long interval is possible with IC 555,but in practical conditions, it is difficult to get more than 3 minutes. If low leakage Tantalum capacitor is used, this can be increased to 5 minutes or more. If the value of the timing capacitor is too high above 470 uF, charging time will be prolonged which will upset the timing cycle and the output remains high even after the desired time is over.
Streampowers
10 W Audio Amplifier Rise
Posted by Okla
Posted on 05:45
The energy provide vital for is eight - 18V DC at one Amp or more. Maximum output energy will only be got with a energy supply of better than 1A at sixteenV DC, and the usage of two ohm audio system (or two by means of four ohm audio system in parallel). However about 4W RMS can also be received with a 12V DC, 1A provide in to a four ohm load.
Smart Chocolate Block Schematic Diagram
Posted by Okla
Posted on 03:45

When light switch S1 is operated for the first time lamp La1, which is linked within the normal way, milds; La2 continues to be darkish. Electrolytic capacitor C1 starts to charge by implys of rectifier diode D1 and resistors R1 and R2 except zener diode D3 habitss, limiting the voltage to about 6.8 V. This voltage is used as a provide for the leisure of the circuit. The 2nd lamp is hooked up via a triac and a fuse (1.5 A, medium speed recommended). The triac is induced by means of T4, which can best happen when T3 does not pull its base down to floor. The first time the circuit is changeed on this is the case, as we shall see beneath.
Smart Chocolate Block Schematic
Transistors T1 and T2 type a bistable flip-flop with a well-defined power-up state. R14 and R15 cause both transistors to be at first turned off. As the voltage throughout C1 upward throughsts, transistor T1, driven by method of resistors R7 and R9, activates. The base pressure for transistor T2, which is supplied by means of D2, the low-pass filter shaped through R6 and C2, and R5, would arrive just a little later, however when T1 turns on it diverts the bottom current far from T2, which subsequently is still fliped off. This state of affairs is stable: the bottom of T3 just isn't pulled down and so this transistor behaviors.
To turn the second lamp on, change S1 is opened and then, inside a 2nd or so, closed again. The impact of this action on the flip-flop is as applys.
When the swap is opened the voltage throughout C1 falls more unexpectedly than the volt-age throughout C2. The primary cause of that is resistor R3, which is directly answerable for the discharge of C1; C2 can only discharge through the relatively high resistance of R5, for the reason that different path is blocked through diode D2. This signifies that T2 is pushed by implys of R5 for one or two seconds longer than T1 is driven by the use of R7 and R9. If right through this time the supply voltage reappears, it could actually not force the bottom of T1 via R7 as T2 is conducting the entire current to ground. This scenario is also steady, as C2 is recharged by manner of D2 and R6.
When T2 habitss it pulls the bottom of T3 to ground, so that this latter transistor flips off. Darlington transistor T4 now behaviors as its base is pulled excessive by the use of R4. T4 now gives the trigger present for the triac by method of present limiting resistor R10, and the 2nd lamp gentles.
T5 and T6 collectively kind a zero-crossing detector. It be certains that the triac is rarely brought on at a second when the AC mains supply is at a excessive voltage point in its cycle. This avoids a speedy inrush present into La2, which might supply rise to considerable radio interference. Also, trigger current is only required for the triac for a small fraction of the length of 1 cycle of the primarys supply. If this present had been drawn constantly from the low voltage supply, C1 would rap-idly discharge; R1 and R2 would need to be significantly decreased in resistance, which would elevate the heat dissipation of the module, perhaps making it infeasible to build the circuit into a plastic ceiling rose.
Using the part values shown the triac is most effective pushed when the instantaneous majors voltage is less than about 15 V in magnitude. The voltage divider fashioned by R11, R12 and R13 swapes on the transistors T5 and T6 when the voltage is larger than +15V or less than –15 V respectively. The collectors of these transistors, which can be connected together, pull the base of T4 right down to floor or to a rather poor voltage when the mains cycle is out of doors the desired segment window.
Any resistors throughout which majors voltages might be dropped are fashioned from two person resistors wired in series to ensure that the maximum voltage specifications of ordinary zero.25 W elements will now not be passed. This applies to R1 and R2, as smartly as R11 and R12. The entire circuit is at majors potentials and nice care must be taken to observe all relevant security precautions in building and installation
Electrical Isolation For I2C Bus
Posted by Okla
Posted on 01:30
When the SDA (Serial DAta) strains on both the left and right lines are 1, the circuit is quiescent and optoisolators IC1 and IC2 are typically not actuated. When the SDA line on the left change intos zero, current wafts throughout the LED in IC1 by means of R2. The SDA line on the proper is then pulled low via D2 and IC1. Optoisolator IC2 does now not transfer this 0 to the left, as a end result of the polarity of the LED in IC2 is the flawed approach round for this level. This arrangement stops the circuit conserving itself in the zero state for ever. As is viewed, the circuit is symmetrical. So, when the SDA line on the proper is 0, this is transferred to the left. The decrease a part of the diagram, meant for the SCL (Serial CLock) line, is the similar to the higher part.
Electrical Isolation For I2C Bus Circuit Diagram
Resistors R1, R4, R5, and R8, are the standard three.3 kΩ pull-up resistors which can be necessary in each I2C line. If these resistors are already existing in other situations within the device, they could additionally be omitted here. The current drawn by way of the circuit is fairly higher than average for the reason that pull-up resistors are shunted by the LEDs within the optoisolators and their series resistors. Nevertheless, it remains throughout the norms laid down in the I2C specification.
http://www.ecircuitslab.com
Cranial Electrotherapy Stimulator
Posted by Okla
Posted on 23:30
Current generated flows through clips placed on the earlobes Output current adjustable from 80 to 600 microAmperes
Owing to the recent launching in Europe of Cranial Electrotherapy Stimulation (CES) portable sets, we have been "Electronically Stimulated" in designing a similar circuit for the sake of hobbyists. CES is the most popular technique for electrically boosting brain power, and has long been prescribed by doctors, mainly in the USA, for therapeutic reasons, including the treatment of anxiety, depression, insomnia, and chemical dependency. CES units generate an adjustable current (80 to 600 microAmperes) that flows through clips placed on the earlobes.
The waveform of this device is a 400 milliseconds positive pulse followed by a negative one of the same duration, then a pause of 1.2 seconds. The main frequency is 0.5 Hz, i.e. a double pulse every 2 seconds. Some people report that this kind of minute specialized electrical impulses contributes to achieve a relaxed state that leaves the mind alert. Obviously we cant claim or prove any therapeutic effectiveness for this device, but if you are interested in trying it, the circuit is so cheap and so simple to build that an attempt can be made with quite no harm.
Circuit diagram:

R1___________1M5 1/4W Resistor
R2___________15K 1/4W Resistor
R3___________100K Linear Potentiometer
R4___________2K2 1/4W Resistor
C1___________330nF 63V Polyester Capacitor
C2___________100µF 25V Electrolytic Capacitor
D1___________3mm. Red LED
IC1___________7555 or TS555CN CMos Timer IC
IC2___________4017 Decade counter with 10 decoded outputs IC
SW1__________SPST Slider Switch
B1____________9V PP3 Battery Clip for PP3 Battery
Two Earclips with wires (see notes)
Circuit operation:
IC1 forms a narrow pulse, 2.5Hz oscillator feeding IC2. This chip generates the various timings for the output pulses. Output is taken at pins 2 & 3 to easily obtain negative going pulses also. Current output is limited to 600µA by R2 and can be regulated from 80 to 600µA by means of R3. The LED flashes every 2 seconds signaling proper operation and can also be used for setting purposes. It can be omitted together with R4, greatly increasing battery life.
- In order to obtain a more precise frequency setting take R1=1M2 and add a 500K trimmer in series with it.
- In this case use a frequency meter to read 2.5Hz at pin 3 of IC1, or an oscilloscope to read 400msec pulses at pins 2, 3 or 10, adjusting the added trimmer.
- A simpler setting can be made adjusting the trimmer to count exactly a LED flash every 2 seconds.
- Earclips can be made with little plastic clips and cementing the end of the wire in a position suited to make good contact with earlobes.
- Ultra-simple earclips can be made using a thin copper foil with rounded corners 4 cm. long and 1.5 cm. wide, soldering the wire end in the center, and then folding the foil in two parts holding the earlobes.
- To ensure a better current transfer, this kind of devices usually has felt pads moistened with a conducting solution interposed between clips and skin.
- Commercial sets have frequently a built-in timer. Timing sessions last usually 20 minutes to 1 hour. For this purpose you can use the Timed Beeper the Bedside Lamp Timer or the Jogging Timer circuits available on this website, adjusting the timing components in order to suit your needs.
Streampowers
1998 Gmc Jimmy Wiring Diagram
Posted by Okla
Posted on 21:15
![]() |
1998 Gmc Jimmy Wiring Diagram |
(click for full size image)
The Part of 1998 Gmc Jimmy Wiring Diagram: power distribution, crankcase ground, sensor signal, tachometer, yellow wire, spark plugs, coll wire, distributor, coil assembly, elect spark, ignition positive voltasge, vehicle control module, IC control, camshaft position sensor, mass air flow sensor, power distribution car, ECU fuse, tachometer output, crank sensor signal, sensor signal, knock sensor, instrument cluster, ignition coil assembly, coil wire.
Tuned Radio Frequency TRF Receiver
Posted by Okla
Posted on 17:30
Superheterodyne receivers have been mass-produced since around 1924,
but for reasons of cost did not become successful until the 1930s.
Before the second world war other, simpler receiver technologies such as
the TRF receiver and the regenerative receiver were still widespread.
The circuit described here is based on the old technology, but
brought up-to-date a The most important part of the circuit is the
input stage, where positive feedback is used to achieve good
sensitivity and selectivity. The first stage is adjusted so that it is
not quite at the point of oscillation. This increases the gain and
the selectivity, giving a narrow bandwidth.
To achieve this,
the potentiometer connected to the drain of the FET must be adjusted
very carefully: optimal performance of the receiver depends on its
setting. In ideal conditions several strong stations should be
obtainable during the day using a 50 cm antenna. At night, several
times this number should be obtainable. The frequency range of the
receiver runs from 6 MHz to 8 MHz. This range covers the 49 m and the
41 m shortwave bands in which many European stations broadcast. Not
bad for such a simple circuit! The circuit employs six transistors. The
first stage is a selective amplifier, followed by a transistor
detector. Two low-frequency amplifier stages complete the circuit.
The
final stage is a push-pull arrangement for optimal drive of the
low-impedance loudspeaker. This circuit arrangement is sometimes called a
‘1V2 receiver’ (one preamplifier, one detector and two audio-frequency
stages). Setting-up is straightforward. Adjust P1 until the point is
reached where the circuit starts to oscillate: a whistle will be heard
from the loudspeaker. Now back off the potentiometer until the whistle
stops. The receiver can now be tuned to a broadcaster. Occasional
further adjustment of the potentiometer may be required after the
station is tuned in. The receiver operates from a supply voltage of
between 5 V and 12 V and uses very little current. A 9 V PP3 (6F22)
battery should give a very long life.
but for reasons of cost did not become successful until the 1930s.
Before the second world war other, simpler receiver technologies such as
the TRF receiver and the regenerative receiver were still widespread.
The circuit described here is based on the old technology, but
brought up-to-date a The most important part of the circuit is the
input stage, where positive feedback is used to achieve good
sensitivity and selectivity. The first stage is adjusted so that it is
not quite at the point of oscillation. This increases the gain and
the selectivity, giving a narrow bandwidth.
To achieve this,
the potentiometer connected to the drain of the FET must be adjusted
very carefully: optimal performance of the receiver depends on its
setting. In ideal conditions several strong stations should be
obtainable during the day using a 50 cm antenna. At night, several
times this number should be obtainable. The frequency range of the
receiver runs from 6 MHz to 8 MHz. This range covers the 49 m and the
41 m shortwave bands in which many European stations broadcast. Not
bad for such a simple circuit! The circuit employs six transistors. The
first stage is a selective amplifier, followed by a transistor
detector. Two low-frequency amplifier stages complete the circuit.
final stage is a push-pull arrangement for optimal drive of the
low-impedance loudspeaker. This circuit arrangement is sometimes called a
‘1V2 receiver’ (one preamplifier, one detector and two audio-frequency
stages). Setting-up is straightforward. Adjust P1 until the point is
reached where the circuit starts to oscillate: a whistle will be heard
from the loudspeaker. Now back off the potentiometer until the whistle
stops. The receiver can now be tuned to a broadcaster. Occasional
further adjustment of the potentiometer may be required after the
station is tuned in. The receiver operates from a supply voltage of
between 5 V and 12 V and uses very little current. A 9 V PP3 (6F22)
battery should give a very long life.
Timer Thermostat Circuit
Posted by Okla
Posted on 13:45
Where Do The Rcd Timer Thermostat Go On The Circuit.
Home Thermostat 1 Jpg.
106 Honeywell Thermostat China 106 Honeywell Thermostat.
Honeywell Pro 3000 4000 Thermostat.
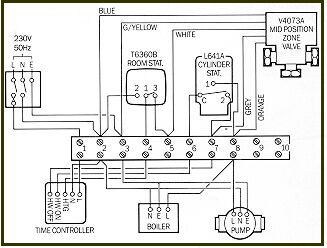
Wiring Diagram Plasterers Forum.
Wiring Diagram And Other Informations For Example Thermostat Wiring.
Wiring Diagram Thr 10 Thermostat Fans Ventilation Ventilation.
How To Wire A 5 Conductor Thermostat To A Carrier Unit Ehow Com.
Always Be Aware Of The Wattage Capacity Limits Of The Thermostat.
To The Thermostat From The Left Wiring To The Roof Is Indicated On.
Pump Controller For Solar Hot Water System
Posted by Okla
Posted on 10:30
This circuit optimises the operation of a solar hot water system. When the water in the solar collector is hotter than the storage tank, the pump runs. The circuit comprises two LM335Z temperature sensors, a comparator and Mosfet. Sensor 1 connects to the solar collector panel while Sensor 2 connects to the hot water panel. Each sensor includes a trimpot to allow adjustment of the output level. In practice, VR1 and VR2 are adjusted so that both Sensor 1 and Sensor 2 have the same output voltage when they are at the same temperature. The Sensor outputs are monitored using comparator IC1.
When Sensor 1 produces a higher voltage than Sensor 2, which means that sensor 1 is at a higher temperature, pin 1 of IC1 goes high and drives the gate of Mosfet Q1. This in turn drives the pump motor. IC1 includes hysteresis so that the output does not oscillate when both sensors are producing a similar voltage. Hysteresis comprises the 1MO feedback resistor between output pin 1 and non-inverting input pin 3 and the input 1kO resistor. This provides a nominal 12mV hysteresis so that voltage at Sensor 1 or Sensor 2 must differ by 12mV for changes in the comparator output to occur.
Circuit diagram:

Pump Controller For Solar Hot Water System
Since the outputs of Sensor 1 and Sensor 2 change by about 10mV/°C, we could say that there is a degree of hysteresis in the comparator. Note that IC1 is a dual comparator with the second unit unused. Its inputs are tied to ground and pin 2 of IC1 respectively. This sets the pin 7 output high. Since the output is an open collector, it will be at a high impedance. Mosfet Q1 is rated at 60A and 60V and is suitable for driving inductive loads due to its avalanche suppression capability. This clamps any inductively induced voltages exceeding the voltage rating of the Mosfet.
The sensors are adjusted initially with both measuring the same temperature. This can be done at room temperature; adjust the trimpots so that the voltage between ground and the positive terminal reads the same for both sensors. If you wish, the sensors can be set to 10mV/°C change with the output referred to the Kelvin scale which is 273K at 0°C. So at 25°C, the sensor output should be set to (273 + 25 = 298) x 10mV or 2.98V.
Note:
The sensors will produce incorrect outputs if their leads are exposed to moisture and they should be protected with some neutral cure silicone sealant. The sensors can be mounted by clamping them directly to the outside surface of the solar collector and on an uninsulated section of the storage tank. The thermostat housing is usually a good position on the storage tank.
Source by : Streampowers